3 takeaways from the OSHA engineered stone fabrication initiative – What does it mean for your business?
December 14, 2023
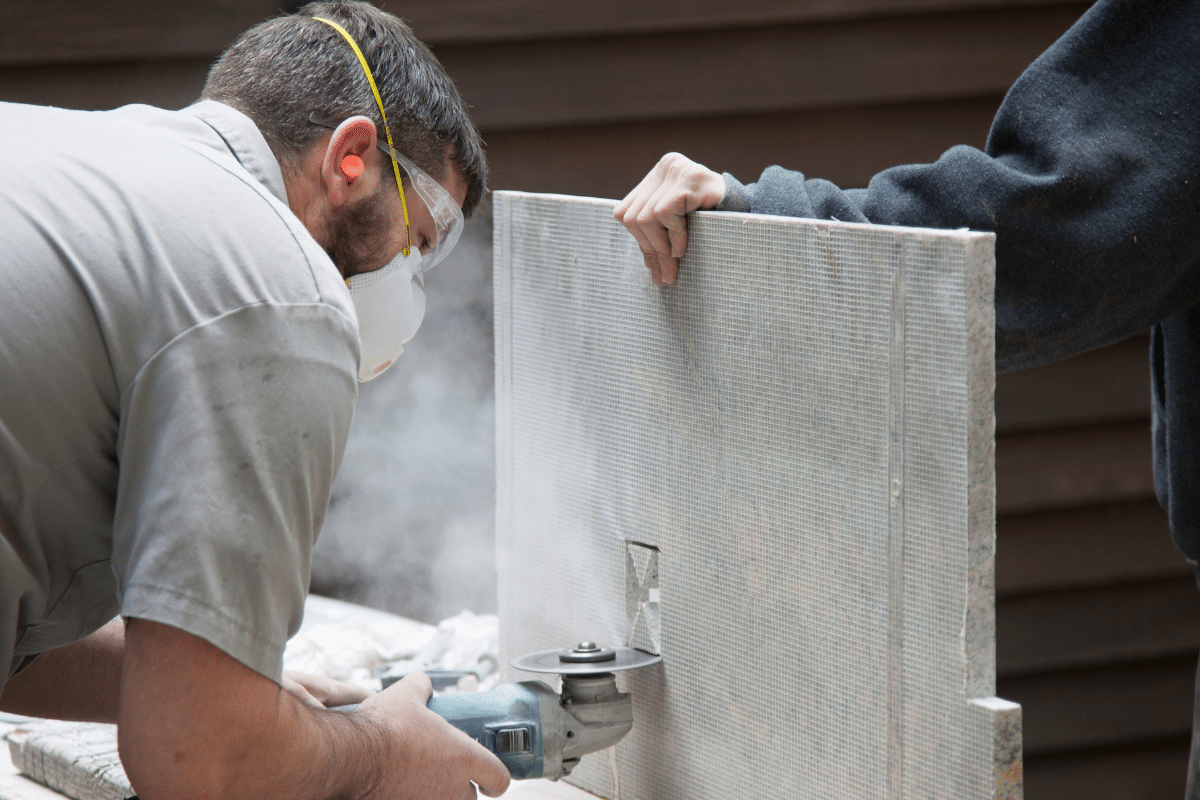
Crystalline silica dust impacts
Crystalline silica dust is an often-overlooked health risk to manufacturers, installers, and fabricators of engineered stone and is created from cutting, sawing, grinding, and drilling the material. Workers who inhale these tiny particles (respirable crystalline silica) which is often invisible under normal lighting, are at an increased risk of developing serious silica-related disease, such as silicosis, lung cancer, chronic obstructive pulmonary disease (COPD), and kidney disease.
In 2023, the engineered stone industry and associated health impacts came to the forefront of public attention after the American Medical Association released the study, “Silicosis Among Immigrant Engineered Stone Countertop Fabrications Workers in California.” In addition, the Los Angeles Times published an article titled, “California workers who cut countertops are dying of an incurable disease”, placing more scrutiny on the industry. Since the release of these publications that note the adverse health effects within the industry, the Occupational Safety and Health Administration (OSHA) has announced a new enforcement and compliance initiative to protect engineered stone fabricators and installers from exposure to respirable crystalline silica dust.
What is the new initiative?
This new initiative is designed to prioritize OSHA-programmed inspections of businesses that engage in engineered stone product manufacturing, fabrication, and installation, as well as brick, stone, and related construction material wholesalers to identify and ensure proper abatement of silica hazards.
3 things to consider about the new engineered stone initiative
- The initiative will affect both the construction and general industry that work with cut stone and engineered stone product manufacturing, fabrication, and installation, as well brick, stone, and related construction material merchant wholesalers.
- OSHA will perform random inspections.
- Companies should be proactive to perform or outsource personal air sampling, determine exposure levels and implement controls.
Random inspections from OSHA will verify employers:
- Have an established written exposure control and respiratory protection plan.
- Provide medical surveillance.
- Have exposure monitoring data and/or objective data to determine controls needed to protect employees.
- Provide proper respiratory protection and dust control measures IAW Table 1 for construction.
- Implemented effective control options and/or safe work methods for general industry that protect workers from silica exposure.
S&ME Industrial Hygiene Services
S&ME is here to support your assessment and monitoring needs for compliance requirements and overall health and safety.
Our teams have experience performing:
- Comprehensive Industrial Hygiene assessments
- Exposure monitoring
- Provide engineering and administrative controls
- Recommend appropriate respiratory protection
- Qualitative or quantitative respiratory protection fit testing
- Safety Program Development and/or Review
Contact Us
For more information, please contact Ryan Butler, MS, CIH, CSP at RyanButler@smeinc.com.
S&ME Principal Industrial Hygienist-Project Manager, Ryan Butler, MS, CIH, CSP has 20+ years of experience in occupational, environmental, health and safety (OEHS) in a wide variety of industries conducting hazard assessments, exposure monitoring, and providing controls to protect workers. Ryan holds two masters degrees in OEHS and Industrial Hygiene fields, and is a certified industrial hygienist (CIH) and certified safety professional (CSP).